With comprehensive
testing resources
The highly demanding requirements of the rail industry require reliable, high-quality electronics. To ensure that every product meets these standards, it is essential to have a perfectly functioning and well-conceived quality management system.
In our process flow charts we define the required measures from the initial design phase to the end of the product life cycle. Each component can be traced through the serial number management system.
In addition, each product undergoes multiple tests and quality control checks in the development process. Our highly qualified employees inspect each device in accordance with the relevant test instructions and the IRIS (ISO TS22163) quality specifications. We also have a comprehensive testing laboratory. The in-depth Gersys testing processes ensure that our components continue to function reliably even under the most extreme environmental conditions.
Tested from top to bottom
We operate our own in-house testing laboratory extensively equipped with modern instrumentation and accepted by leading rail vehicle manufacturers. The in-depth Gersys testing processes verify that our components function precisely even under the most extreme environmental conditions. That means they can be counted on to deliver reliable performance and exact data even in icy cold conditions of -40°C or extreme heat of +85°C.
And full immunity against electromagnetic interference is also part of the package. Devices from Gersys not only comply with the European Railway Standards EN50155 / EN50121-3-2, they also can be produced to meet customer-specific or country-specific requirements.
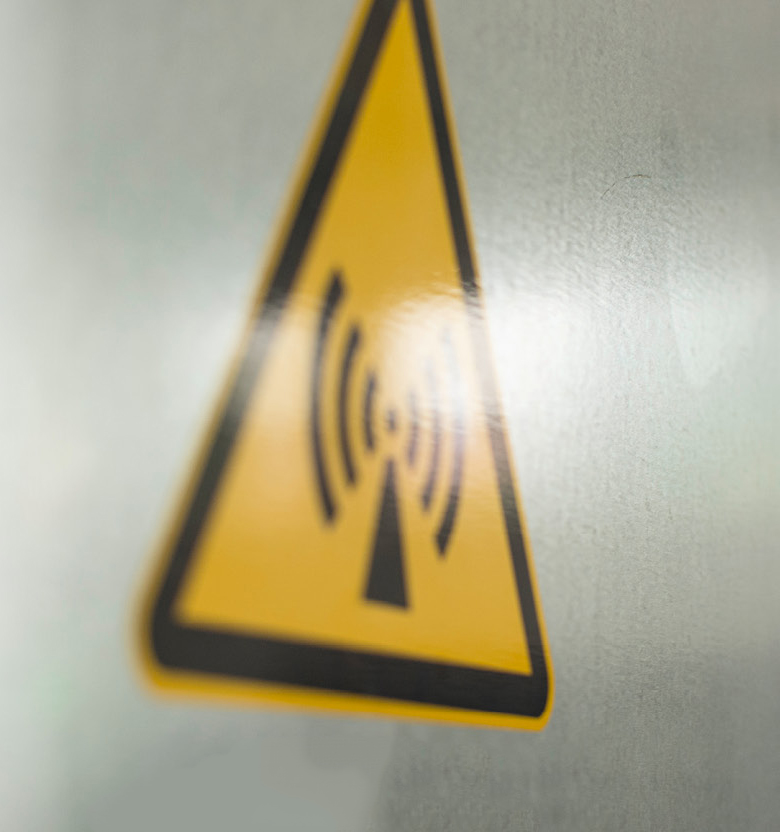
Our measurements
in detail
Our in-house testing laboratory supports the following measurements:
Interference emission
- Conducted emissions of 9 kHz to 30 MHz (in accordance with EN55016 and EN55022)
- Emissions (H and E fields) of 30 MHz to 6 GHz (in accordance with EN55016)
Interference immunity
- Radiation from 80 MHz to 6 GHz, field strengths up to 30 V/m (according to EN6100, 4-3)
- Electrostatic discharge (ESD), surge and burst
- Test set-up according to EN61000-4-2; 4-4
Climate simulations
- Cold conditions to -40°C, dry heat up to +85°C (technically possible test interval -70°C to 180°C)
- Relative humidity 5 - 98%
- Tests according to IEC68-2-x
Shock and vibration test
- Durability testing with random vibration signals
- Shock testing according to IEC 61373
- Sine vibration testing
- Resonance point search
Burn-in testing
- Passive run-in testing. In passive run-in testing, the test units are run-in at an elevated ambient temperature for at least 48 hours.
- Active burn-in testing. In the temperature chamber, the test units are subjected to a "stress" temperature profile that approximates the customer's specification. This procedure also allows for testing the switch-on behavior at low temperatures.
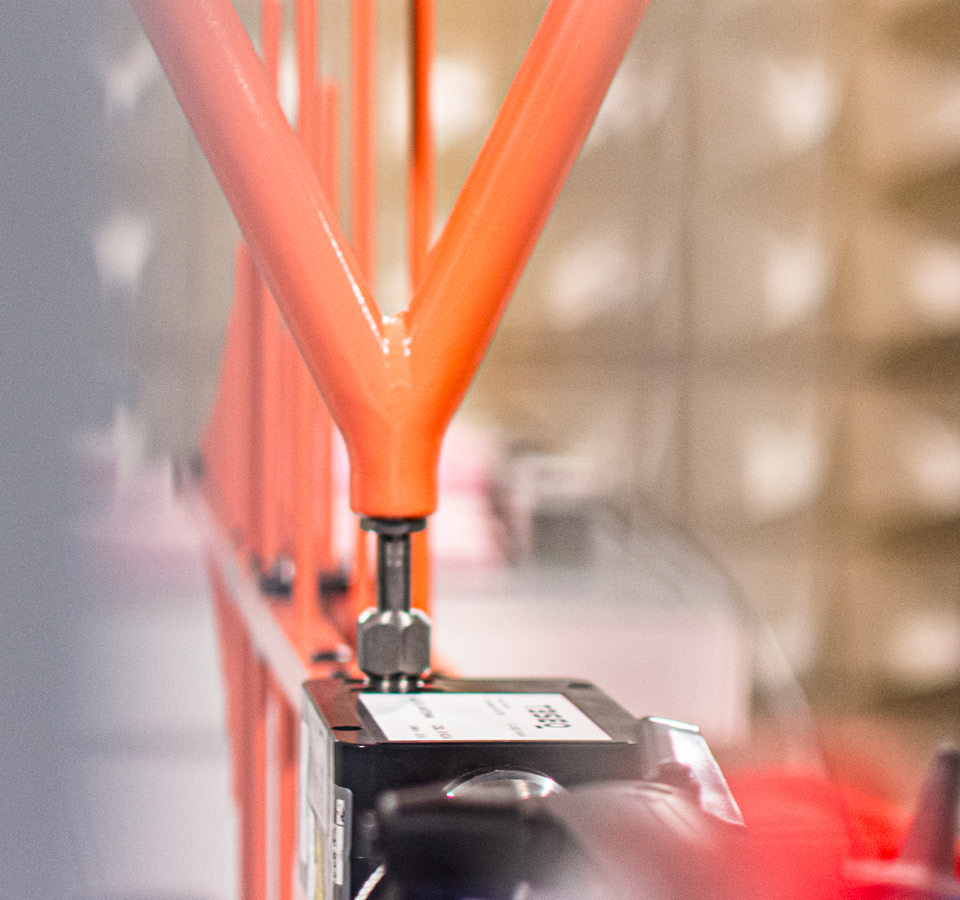